Casting involves pouring molten metal into molds to form shapes, allowing for complex designs. Forging reshapes solid metal ingots using heat and mechanical force, resulting in stronger, more durable components due to the refined grain structure.
In the world of manufacturing, forging and casting are two prominent methods used to shape metals and materials. These techniques, though they share the common goal of producing strong, durable components, differ significantly in their processes, applications, and outcomes. Understanding these differences is crucial for selecting the appropriate method for specific industrial applications. Here, we delve into the seven key differences between forging and casting, providing a comprehensive analysis to aid in your decision-making process.
1. Process Fundamentals
Forging
Forging involves the deformation of metal through the application of compressive forces. This process can be executed at various temperatures, typically categorized as hot forging or cold forging. Hot forging is performed at high temperatures, making the metal more malleable and easier to shape. Cold forging, on the other hand, is done at or near room temperature and typically requires more force.
Casting
Casting is the process of pouring molten metal into a mold where it solidifies into a specific shape. This method is highly versatile and can produce complex shapes that would be challenging or impossible to achieve through forging. The casting process includes several steps: melting the metal, pouring it into a mold, allowing it to cool and solidify, and finally, removing the cast part from the mold.
2. Material Properties and Strength
Forging
Forged parts are generally stronger and more reliable than cast parts. This is because the forging process aligns the grain structure of the metal, enhancing its mechanical properties and producing parts with higher tensile strength and impact resistance. The absence of internal voids or porosity in forged parts also contributes to their superior strength.
Casting
Casting does not manipulate the grain structure of the metal in the same way forging does. As a result, cast parts may contain internal defects such as porosity, which can weaken the material. However, casting allows for a wider range of alloys and materials, including those that are difficult or impractical to forge.
3. Dimensional Accuracy and Surface Finish
Forging
Forging typically results in parts with better dimensional accuracy and superior surface finish compared to casting. This is due to the controlled deformation of the material and the finishing processes that can be applied post-forging, such as machining and polishing. Forged parts often require less secondary machining than cast parts.
Casting
Casting can achieve complex shapes and intricate details that are difficult with forging, but it may compromise on surface finish and dimensional accuracy. The cooling and solidification process can lead to shrinkage, warping, and surface irregularities that necessitate further machining and finishing operations.
4. Production Speed and Efficiency
Forging
Forging can be faster for producing parts, especially in high-volume manufacturing scenarios. The process, once set up, can rapidly produce a large number of parts with consistent quality. The primary time investment lies in the initial setup and die creation.
Casting
Casting can be slower due to the time required for melting the metal, pouring, cooling, and solidifying. Additionally, the creation of molds can be time-consuming, especially for complex shapes. However, once the molds are made, casting can efficiently produce large quantities of parts, particularly when using permanent molds or automated casting lines.
5. Design Flexibility and Complexity
Forging
Forging is generally limited in terms of design complexity. The process is best suited for simpler, geometrically straightforward parts. While advanced forging techniques can produce more complex shapes, they are often not as intricate as those achievable with casting.
Casting
Casting offers greater design flexibility and can produce highly complex and detailed shapes. Intricate internal geometries, undercuts, and thin walls are more easily achieved with casting. This makes casting ideal for parts with complex designs that would be challenging to forge.
6. Cost Considerations
Forging
The initial cost for forging can be high due to the expense of creating dies and the machinery involved. However, the per-unit cost decreases significantly with high-volume production. Forged parts also tend to have lower long-term maintenance costs due to their superior strength and durability.
Casting
Casting can be more cost-effective for low-volume production runs and highly complex parts. The cost of molds and the casting process itself can vary widely based on the material and complexity of the part. However, the presence of potential defects in cast parts can lead to higher quality control and maintenance costs over time.
7. Applications and Industries
Forging
Forging is widely used in industries where strength, durability, and reliability are paramount. Common applications include automotive components, aerospace parts, industrial machinery, and tools. Forged parts are often found in high-stress environments where failure is not an option.
Casting
Casting is prevalent in industries requiring complex shapes and intricate designs, such as the automotive sector (engine blocks, cylinder heads), the arts (sculptures, decorative items), and large-scale manufacturing (pipes, valves). Casting is also favored in producing parts from materials that are difficult to forge.
Conclusion About Differences Between Forging and Casting
Choosing between forging and casting depends on various factors, including the required material properties, part complexity, production volume, and cost constraints. Forging offers superior strength and reliability, making it ideal for high-stress applications. Casting, with its design flexibility and ability to produce complex shapes, is better suited for intricate parts and diverse materials. Understanding these differences will guide you in selecting the best manufacturing method for your specific needs.
Related Posts:
7 Easy Steps to Understand the Casting Process
Die Casting Process: A Complete Guide in 10 Easy Steps
The Complete Metal Forging Guide: All About Forging
FAQs:
What are the main advantages of forging over casting?
Forging generally results in parts with superior strength and reliability due to the alignment of the metal’s grain structure during the deformation process. Forged parts also tend to have better dimensional accuracy and surface finish, which reduces the need for secondary machining. Additionally, forging is often more cost-effective for high-volume production runs.
Can casting achieve the same mechanical properties as forging?
While casting can produce complex shapes and detailed designs, it typically does not achieve the same mechanical properties as forging. Cast parts may contain internal defects such as porosity, which can weaken the material. Forging, by aligning the grain structure, enhances tensile strength and impact resistance, resulting in stronger and more durable parts.
Which process is more suitable for producing complex shapes, forging or casting?
Casting is more suitable for producing complex shapes and intricate details. The process of pouring molten metal into molds allows for the creation of parts with intricate geometries, undercuts, and thin walls that would be challenging to achieve through forging. Forging is better suited for simpler, geometrically straightforward parts.
What factors should be considered when choosing between forging and casting?
When choosing between forging and casting, consider factors such as the required material properties, part complexity, production volume, and cost constraints. Forging is ideal for applications requiring high strength and durability, while casting is preferred for complex designs and parts made from materials that are difficult to forge.
How do the costs of forging and casting compare?
The initial costs for forging can be high due to the expense of creating dies and the machinery involved. However, the per-unit cost decreases significantly with high-volume production. Casting can be more cost-effective for low-volume production runs and highly complex parts, but the presence of potential defects in cast parts can lead to higher quality control and maintenance costs over time.
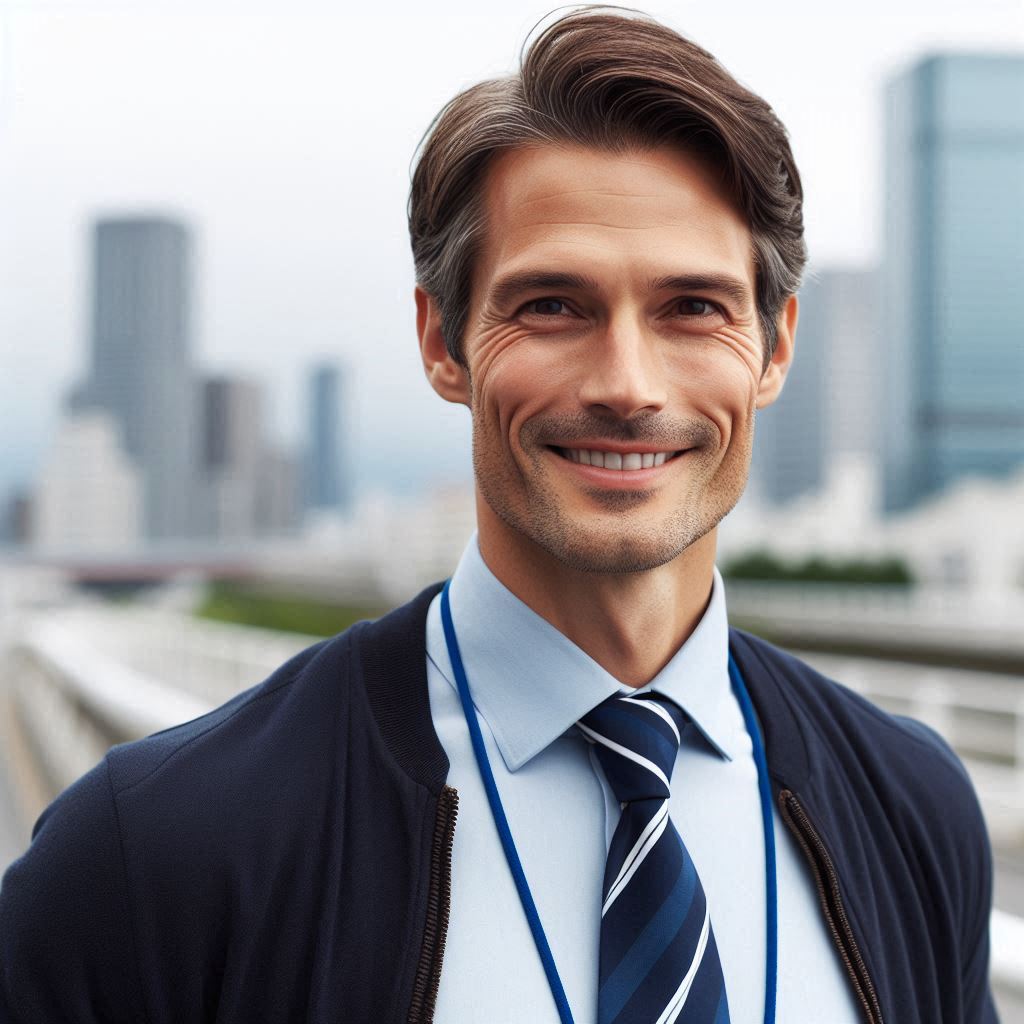
HA Chaudhary is an experienced engineer with 15 years in the mechanical and industrial sectors. Holding advanced degrees and multiple certifications in engineering, he combines technical expertise with a passion for writing to provide valuable insights into engineering innovations and business strategies. His content empowers professionals to excel in their fields and stay updated with the latest industry trends.