Forging is a metalworking process where heated metal is shaped through compressive forces. It enhances the material’s strength, grain structure, and mechanical properties by aligning its internal structure, yielding durable components for various industrial applications.
Open Die Forging Meaning/Definition:
Open die forging, also known as free forging, is a metal shaping process where the workpiece is hammered or pressed between flat or shaped dies. Unlike closed die forging, the metal is not fully confined, allowing it to flow laterally. This process is highly versatile, as it can be used to produce a wide range of shapes and sizes, from simple to complex geometries. Open die forging is particularly suitable for large components or parts with irregular shapes. It offers advantages such as improved grain structure, enhanced mechanical properties, and reduced material waste. Common applications include shafts, discs, rings, and bars used in industries like aerospace, automotive, and oil and gas.
Closed Die Forging Meaning/Definition:
Closed die forging, also known as impression die forging, is a metal shaping process where the workpiece is formed within the confines of two dies. The dies contain the desired shape, and the metal is compressed between them to fill the die cavities. This process allows for precise control over the final shape and dimensions of the forged part. Closed die forging is capable of producing complex geometries with high accuracy and repeatability. It offers advantages such as improved mechanical properties, tight tolerances, and minimal machining requirements. Common applications include automotive components, aerospace parts, hand tools, and industrial machinery.
Roll Forging Meaning/Definition:
Roll forging is a metal shaping process where the workpiece is continuously squeezed between rotating rolls to achieve the desired shape. The rolls exert compressive forces on the metal, causing it to deform and take on the shape of the roll profiles. This process is particularly suited for producing long lengths of cylindrical or tapered shapes with consistent cross-sectional dimensions. Roll forging offers advantages such as high production rates, improved material utilization, and enhanced mechanical properties due to grain flow alignment. Common applications include shafts, axles, gears, and threaded rods used in automotive, aerospace, and construction industries.
Swaging Meaning/Definition:
Swaging is a metal forming process where the diameter of a rod or tube is reduced by forcing it through a die or series of dies. The dies exert radial compressive forces on the workpiece, causing it to flow and conform to the shape of the die cavities. This process is commonly used to produce tapered or shaped profiles with precise dimensions and surface finishes. Swaging offers advantages such as improved mechanical properties, dimensional accuracy, and surface integrity. Common applications include the manufacture of pipes, tubes, cables, and fasteners used in various industries such as construction, automotive, and aerospace.
Upset Forging Meaning/Definition:
Upset forging, also known as heading or end forging, is a metal shaping process where the length of the workpiece is increased while its cross-sectional area is decreased. This is achieved by applying compressive forces to one end of the workpiece, causing it to plastically deform and thicken in the upset region. Upset forging is commonly used to create heads, shoulders, or enlarged sections on rods, bolts, pins, and other fasteners. It offers advantages such as improved strength, grain structure refinement, and dimensional accuracy. Common applications include automotive bolts, rivets, nails, and construction anchors.
Press Forging Meaning/Definition:
Press forging is a metal shaping process where compressive forces are applied to the workpiece using a mechanical or hydraulic press. The press applies controlled pressure to deform the metal and shape it into the desired form. Press forging can be performed using either closed or open dies, depending on the complexity of the part and the required precision. This process offers advantages such as high production rates, uniform deformation, and excellent dimensional accuracy. It is suitable for producing a wide range of components, from simple to complex geometries, with improved mechanical properties and surface finishes. Common applications include automotive crankshafts, connecting rods, gears, and hydraulic components.
Benefits Of Forging:
Strength and Durability:
Forging increases the strength of metal components by aligning the grain structure, resulting in superior toughness and resistance to fatigue, impact, and wear. This ensures reliability and longevity in demanding applications, such as automotive, aerospace, and heavy machinery.
Improved Metallurgical Properties:
The controlled deformation and grain flow during forging refine the microstructure of the metal, enhancing its mechanical properties like hardness, ductility, and toughness. This leads to high-performance parts with consistent quality, reducing the risk of material failure and enhancing overall product performance.
Precision and Dimensional Accuracy:
Forging allows for precise control over the shape and dimensions of components, resulting in tight tolerances and minimal machining requirements. This ensures conformity to design specifications, reduces material waste, and streamlines manufacturing processes, improving efficiency and cost-effectiveness.
Enhanced Structural Integrity:
The absence of porosity and other internal defects in forged parts ensures superior structural integrity and reliability under extreme conditions, such as high temperatures, pressures, or corrosive environments. This makes forged components ideal for critical applications where safety and performance are paramount.
Cost Efficiency:
While initial tooling costs may be higher, forging offers long-term cost savings through increased material utilization, reduced scrap, and minimal secondary operations. The durability and longevity of forged parts also contribute to lower lifecycle costs, making forging a cost-effective manufacturing solution over the product’s lifespan.
Design Flexibility:
Forging allows for the production of complex shapes and geometries that may be difficult or impossible to achieve using other manufacturing methods. This design flexibility enables innovation and customization, empowering engineers to optimize component performance and functionality for specific applications.
Environmental Sustainability:
Compared to other manufacturing processes, forging typically generates less waste and consumes less energy, making it a more environmentally friendly option. The ability to recycle and reuse scrap material further reduces the environmental footprint of forging operations, aligning with sustainable manufacturing practices and corporate social responsibility initiatives.
Related Posts:
7 Key Differences Between Forging and Casting
7 Easy Steps to Understand the Casting Process
Die Casting Process: A Complete Guide in 10 Easy Steps
FAQs:
What is forging, and how does it differ from other metalworking processes?
Forging is a metalworking process where heated metal is shaped through compressive forces. It differs from other processes like casting, which involves pouring molten metal into a mold, and machining, which involves removing material from a solid block.
What are the advantages of forging over casting or machining?
Forging offers superior strength, improved metallurgical properties, and enhanced dimensional accuracy compared to casting. It also produces parts with better structural integrity and surface finish. Compared to machining, forging typically requires less material removal, resulting in less waste and higher material utilization.
What types of metals are commonly forged, and are there any limitations to the materials used?
Commonly forged metals include steel, aluminum, titanium, and various alloys. While most metals can be forged, the process is most effective for materials with good ductility and forgeability. Some materials may have limitations due to their brittleness or difficulty in forming complex shapes.
How does the forging process contribute to the strength and durability of metal components?
Forging aligns the grain structure of the metal, which increases its strength, toughness, and resistance to fatigue and impact. The controlled deformation during forging also eliminates internal defects, ensuring superior structural integrity and durability in the finished components.
What industries commonly utilize forged parts, and what are some notable applications within those industries?
Industries such as automotive, aerospace, oil and gas, and construction commonly utilize forged parts. Notable applications include engine components (e.g., crankshafts, connecting rods), aircraft landing gear, industrial machinery components, and high-pressure fittings and valves.
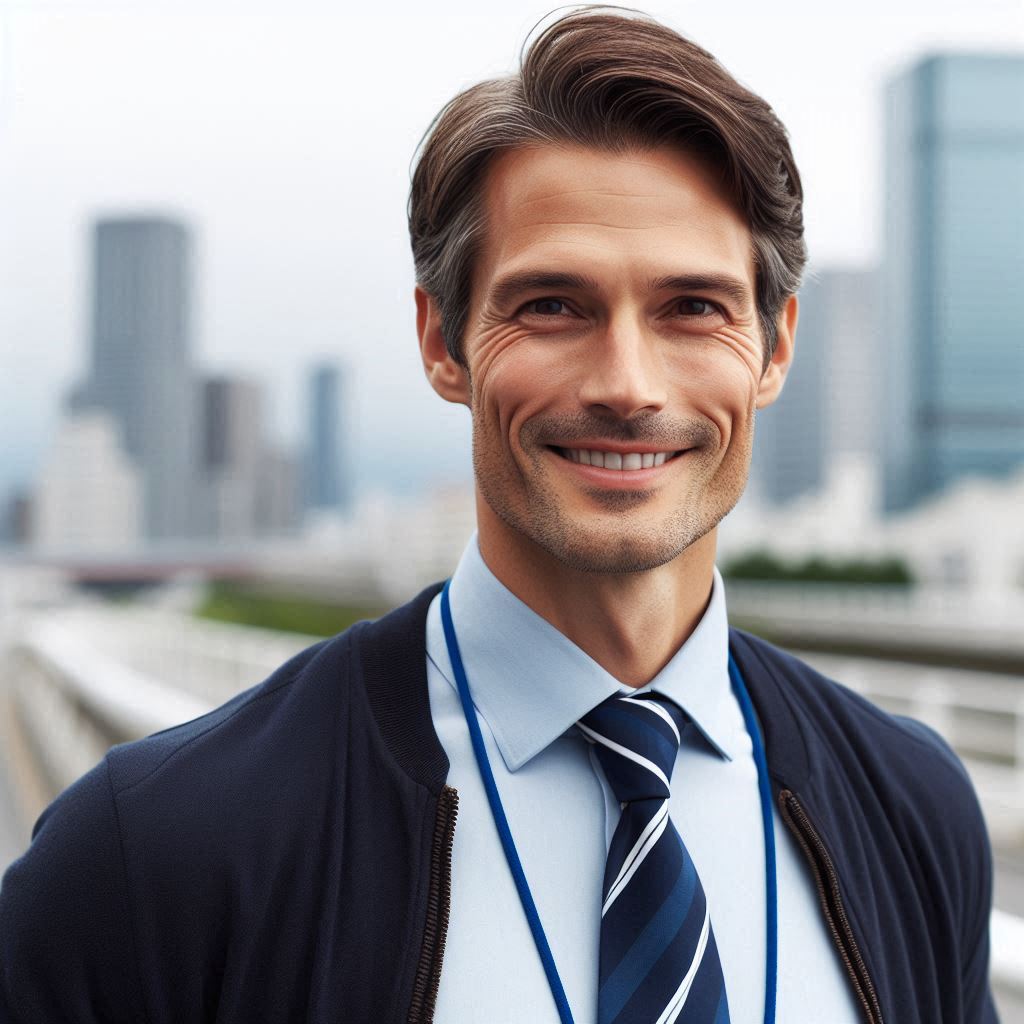
HA Chaudhary is an experienced engineer with 15 years in the mechanical and industrial sectors. Holding advanced degrees and multiple certifications in engineering, he combines technical expertise with a passion for writing to provide valuable insights into engineering innovations and business strategies. His content empowers professionals to excel in their fields and stay updated with the latest industry trends.