Metal forging stands as a timeless testament to human ingenuity and craftsmanship, a tradition that has endured for centuries and continues to shape the world we inhabit. From the earliest civilizations to the present day, forging has been integral to the development of society, yielding tools, weapons, and machinery that have propelled humanity forward. In this comprehensive guide, we embark on a journey through the annals of history, tracing the evolution of metal forging from its ancient origins to its modern applications. Delving deep into the art and science of forging, we uncover the techniques, principles, and innovations that have made it a cornerstone of manufacturing and engineering.
Join us as we explore the rich tapestry of metal forging, from its humble beginnings to its indispensable role in shaping the world as we know it.
Understanding Metal Forging
What is Metal Forging?
Metal forging is a meticulous manufacturing process deeply ingrained in the annals of human history. It involves the art of shaping metal through the application of localized compressive forces. This intricate procedure typically commences with the heating of the metal to elevated temperatures, rendering it malleable. Subsequently, precise pressure is exerted to deform the metal, meticulously crafting it into the desired form. The hallmark of this process lies in its ability to imbue parts with unparalleled strength, durability, and exceptional mechanical properties, making it a cornerstone of modern engineering.
History of Metal Forging
The rich tapestry of metal forging unfurls across the corridors of time, tracing its origins to the cradle of civilization. Ancient societies such as the Mesopotamians, Egyptians, and Greeks laid the foundational stones of this venerable craft, harnessing its power to fashion tools, weapons, and ornate artifacts. These early artisans, with their ingenuity and skill, forged a path of innovation, refining and perfecting the techniques over generations. As civilizations flourished and empires rose and fell, the art of metal forging persevered, evolving in tandem with human progress. With each passing era, new advancements in metallurgy and technology propelled the craft to greater heights, shaping the destiny of nations and leaving an indelible mark on history.
Applications of Metal Forging
Automotive:
In the realm of automotive engineering, metal forging reigns supreme as the cornerstone of performance and reliability. From the heart of the engine to the wheels that grip the road, forged components play a pivotal role in ensuring optimal functionality and longevity. Crankshafts, connecting rods, and gears, crafted with precision and finesse, withstand the punishing forces of combustion and motion, delivering power and torque with unwavering consistency. With forged components at the helm, automotive engineers navigate the road ahead with confidence, knowing that every part is forged in the crucible of excellence.
Aerospace:
The boundless expanse of the sky beckons with the promise of innovation and discovery, and in this celestial realm, metal forging stands as a beacon of progress. Within the aerospace industry, forged parts soar to new heights, shaping the very fabric of flight with their impeccable craftsmanship and unrivaled performance. From the towering landing gear that cushions the descent to the turbine disks that harness the fury of jet propulsion, forged components form the backbone of modern aviation, ensuring safety, efficiency, and reliability with every ascent and descent.
Oil and Gas:
Beneath the earth’s surface lies a wealth of resources waiting to be harnessed, and in the realm of oil and gas exploration, metal forging plays a pivotal role in unlocking this treasure trove. From the depths of drilling rigs to the sprawling networks of pipelines that traverse continents, forged components withstand the harsh conditions of extraction, production, and transportation with unwavering fortitude. Valves that control the flow of precious fluids, pipelines that carry them across vast distances, and drilling equipment that pierces the earth’s crust, all rely on the strength, durability, and resilience of forged steel to keep the wheels of industry turning.
Construction:
In the ever-evolving landscape of construction, metal forging stands as a stalwart guardian of structural integrity and longevity. From towering skyscrapers to sprawling infrastructure projects, forged steel forms the backbone of modern construction, offering unmatched strength, durability, and resistance to corrosion. Structural components, fasteners, and fittings forged with precision and care provide the scaffolding upon which the built environment rises, enduring the passage of time with grace and resilience. Whether it’s the framework of a bridge or the skeleton of a high-rise, forged steel ensures that every structure stands tall and proud, a testament to human ingenuity and craftsmanship.
Defense:
In the crucible of conflict, where the fate of nations hangs in the balance, metal forging emerges as a formidable ally in the arsenal of defense. Military applications of metal forging encompass a diverse array of components, from the explosive power of artillery shells to the precision-guided accuracy of missile components. Armored vehicle parts forged with strength and resilience withstand the ravages of battle, offering protection to those who serve on the front lines. With forged steel at their disposal, defense forces around the world stand ready to confront any challenge with unwavering resolve and unyielding strength.
Related Posts:
Exploring 10 Types of File Tools (Pictures): Materials and Uses
Conclusion
Metal forging stands as a timeless testament to the ingenuity and resilience of human craftsmanship, weaving its way through the annals of history to shape the world as we know it today. Across diverse industries spanning automotive, aerospace, oil and gas, construction, and defense, the art of forging continues to exert its influence, producing components of unparalleled strength, durability, and precision. With each hammer blow and press of the die, forged parts emerge from the crucible of the forge, ready to withstand the trials of time and the rigors of modern engineering.
As we look to the future, the principles and applications of metal forging remain as relevant as ever, offering boundless opportunities for innovation and progress in the pursuit of excellence.
FAQs About Metal Forging:
What is metal forging?
Metal forging is a manufacturing process that involves shaping metal using localized compressive forces. It typically entails heating the metal to a high temperature and then applying pressure to deform it into the desired shape.
What are the advantages of metal forging?
Metal forging offers numerous advantages, including superior strength and durability, improved mechanical properties, cost-effectiveness in the long run, and unparalleled design flexibility.
What industries utilize metal forging?
Metal forging finds application across various industries, including automotive, aerospace, oil and gas, construction, and defense. It is used to produce critical components such as crankshafts, turbine disks, drilling equipment, structural members, and armored vehicle parts.
What are the different types of metal forging processes?
There are several types of forging processes, including open-die forging, closed-die forging, impression-die forging, and cold forging. Each process is suited to specific applications and materials, offering unique advantages in terms of efficiency and precision.
How does metal forging compare to other manufacturing methods?
Metal forging stands out for its ability to produce parts with exceptional strength, durability, and mechanical properties compared to other manufacturing methods such as casting and machining. Additionally, forging often results in higher material utilization and reduced machining requirements, making it a cost-effective choice in the long run.
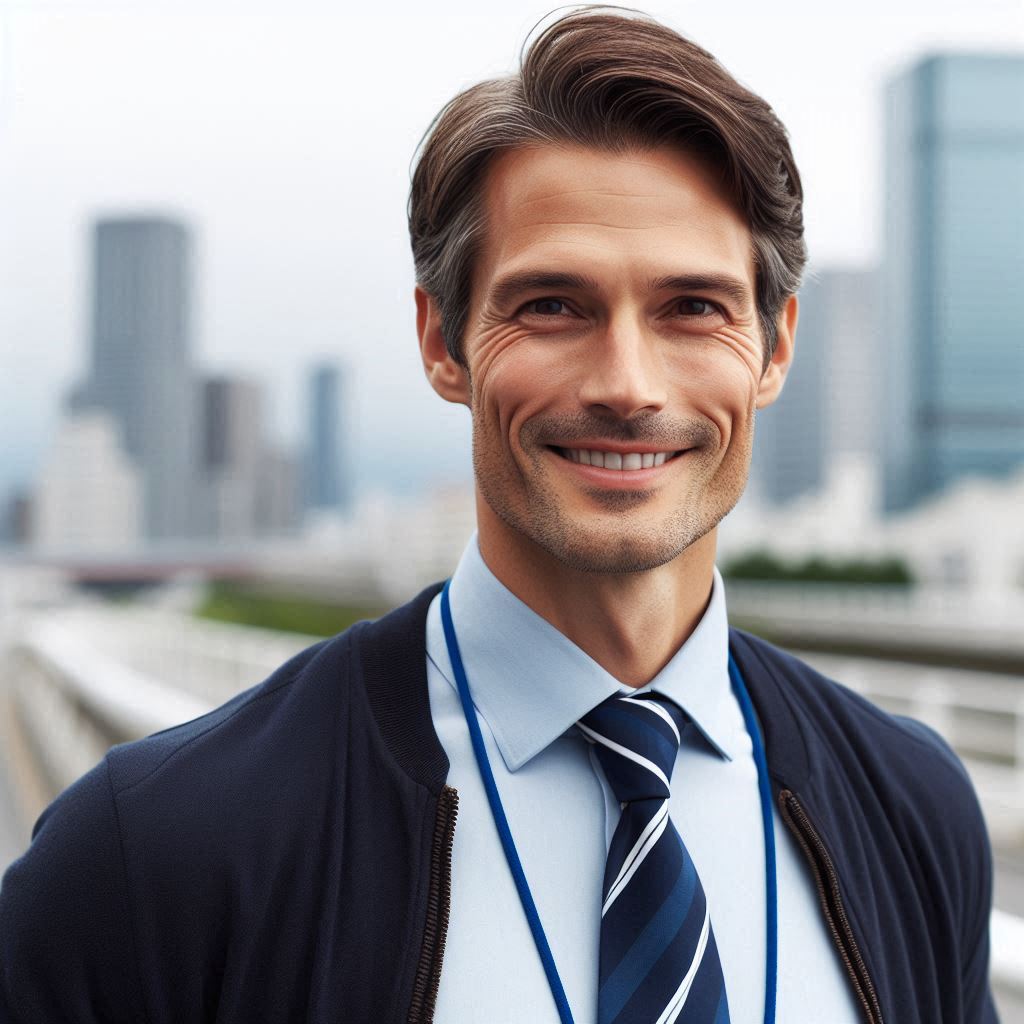
HA Chaudhary is an experienced engineer with 15 years in the mechanical and industrial sectors. Holding advanced degrees and multiple certifications in engineering, he combines technical expertise with a passion for writing to provide valuable insights into engineering innovations and business strategies. His content empowers professionals to excel in their fields and stay updated with the latest industry trends.