Precision machining is a manufacturing process that creates intricate parts with high accuracy and tight tolerances. It involves using advanced machinery and techniques to shape raw materials like metal into precise components for various industries such as aerospace, automotive, and medical.
In the vast landscape of manufacturing, precision machining emerges as cornerstone, redefining the essence of crafting quality products. Precision machining, a technique vital for manufacturing, goes beyond the ordinary to create components with exceptional accuracy and detail. As we delve into the world of Precision Machining, It is crucial to recognize its profound impact on product excellence. This method, characterized by meticulous craftsmanship, ensures that every piece meets exact specifications, elevating the standards of modern manufacturing.
Precision Machining is not just process, It’s a commitment to perfection, where each cut and contour is executed with the utmost accuracy. Join us on this exploration of Precision Machining, where precision is not just term, It’s a transformative force shaping the future of manufacturing.
Table of Contents
TogglePrecision Machining Definition:
Precision machining is a manufacturing process that involves removing material from a workpiece to create highly accurate and detailed parts. It uses advanced machinery, such as lathes, mills, and grinders, often controlled by computer numerical control (CNC) systems, to achieve extremely tight tolerances and precise dimensions. This process is commonly used to produce components for industries like aerospace, automotive, and medical devices, where accuracy and quality are critical. Precision machining works with various materials, including metals, plastics, and composites, ensuring that each part meets exact specifications. By delivering exceptional consistency and performance, precision machining plays a vital role in creating the complex parts and systems used in modern technology and engineering.
What is Precision Machining?
Precision Machining is the heartbeat of manufacturing excellence, defining realm where accuracy and meticulous craftsmanship converge to create the high quality products.
Defining Precision Machining:
Precision Machining is more than process, It is the commitment to crafting intricate components with unparalleled accuracy. At its core, it involved the use of advanced machinery and tools to cut, shape and form materials into precise specifications, ensuring each piece meets stringent quality standards.
Key Characteristics and Principles of Precision Machining:
The hallmark of Precision Machining lies in its attention to detail and adherence to exact the specifications. It operates on the principles of accuracy, consistency and repeatability. Utilizing cutting edge technology, It transforms raw materials into components that form the building blocks of diverse industries.
Role of Precision Machining in Achieving High-Quality Products:
In the grand tapestry of manufacturing, It plays the pivotal role in achieving products of exceptional quality. From aerospace components to medical devices, its impact is felt across industries. Each cut and contour is executed with precision, contributing to the overall excellence of the finished product.
In this exploration, we delve into world where precision is not just requirement but the transformative force. It is journey where every turn of the lathe and every pass of the cutter is step towards crafting products that redefine the benchmarks of quality manufacturing.
Types of Precision Machining
Precision Machining unfolds into the spectrum of techniques, each contributing to the meticulous crafting of components that define modern manufacturing.
Precision CNC Machining: Understanding Computer Numerical Control:
At the forefront stands CNC Machining, where precision meets automation. Computer Numerical Control (CNC) empowers machinery to execute the intricate tasks with unparalleled accuracy. This method transforms digital designs into tangible products, ensuring precision at every turn of the cutter.
Turning and Milling: Versatile Precision Machining Techniques:
Turning and Milling emerge as the workhorses of precision machining, offering versatility in crafting components. Turning, revolving materials against cutting tools and milling, removing material through rotary cutters, together form a dynamic duo capable of creating myriad of intricate shapes and designs.
Precision Electrical Discharge Machining (EDM): Achieving Precision through Electrical Sparks:
EDM takes the unique approach, utilizing electrical discharges to shape materials. By eroding conductive materials with controlled sparks, EDM achieves precision in intricate designs that may be challenging for traditional machining methods.
Precision Machining Grinding Processes: Achieving Fine Surface Finishes:
Precision in surface finishes finds its epitome in Grinding Processes. Through abrasion, this technique refines surfaces to exact specifications. From smoothing rough edges to achieving mirror-like finishes, grinding ensures the desired texture and precision.
As we navigate through these machining techniques, the common thread is evident, an unwavering commitment to achieving the utmost precision in every component, underscoring the significance of precision machining in the manufacturing landscape.
Discover the different manufacturing process types, complete with real-world examples, in this detailed guide. Gain insights into the methods shaping industries today. Read the full post for in-depth knowledge!
Different Precision Machining Methods
Precision machining involves a variety of techniques used to create components with high accuracy and tight tolerances. Here are some of the most common precision machining methods:
CNC Machining
CNC (Computer Numerical Control) machining is one of the most widely used methods in precision machining. This process involves automated control of machine tools through pre-programmed software, allowing for highly accurate cuts and shapes. CNC machines can work with various materials, including metals, plastics, and composites, and are used for drilling, turning, milling, and grinding.
Turning
Turning is a method where the workpiece rotates while a cutting tool moves along its axis to remove material and create cylindrical parts. This process is typically performed on a lathe. Precision turning is essential for producing parts like shafts, pins, and bushings.
Milling
Milling uses rotating cutting tools to remove material from a workpiece. It can create complex shapes, holes, and slots with a high degree of precision. Milling machines can be horizontal or vertical and are often controlled by CNC systems for enhanced accuracy.
Grinding
Grinding is a machining process that uses an abrasive wheel to remove small amounts of material from the surface of a workpiece, achieving extremely fine finishes and precise dimensions. It is commonly used for achieving tight tolerances and smooth surfaces in metalworking.
Electrical Discharge Machining (EDM)
EDM is a non-contact process that uses electrical sparks to erode material from a workpiece. It is ideal for machining hard materials and complex shapes that would be difficult or impossible to achieve with traditional cutting methods. There are two main types of EDM: wire EDM and sinker EDM.
Laser Cutting
Laser cutting uses a focused laser beam to cut or engrave materials with high precision. It is particularly effective for cutting metals, plastics, and ceramics with intricate designs or tight tolerances. Laser cutting offers speed and accuracy, making it ideal for both prototyping and mass production.
Waterjet Cutting
Waterjet cutting uses a high-pressure stream of water, often mixed with an abrasive, to cut through materials. This method is highly precise and can cut various materials, including metals, plastics, stone, and composites, without generating heat, which prevents material distortion.
Drilling
Drilling is a common machining method used to create cylindrical holes in a workpiece. Precision drilling ensures accurate hole placement and diameter, which is critical in applications like aerospace and automotive manufacturing.
Broaching
Broaching is used to remove material using a multi-tooth cutting tool. It is particularly useful for creating complex internal shapes, such as splines, keyways, and gear teeth. Broaching offers high accuracy and surface finish, making it ideal for producing precision components.
Lapping and Honing
Lapping and honing are finishing processes used to improve surface finishes and achieve extremely tight tolerances. Lapping involves rubbing two surfaces together with an abrasive compound, while honing uses an abrasive stone to achieve precise dimensions and improve surface quality.
Each precision machining method serves a specific purpose depending on the material, design, and tolerances required. CNC machining, turning, milling, and grinding are among the most commonly used techniques, but advanced methods like EDM, laser cutting, and waterjet cutting are also crucial for complex or hard-to-machine components. Selecting the right method depends on the specific requirements of the project, including material type, precision needs, and production volume.
Uncover everything you need to know about manufacturing processes in this comprehensive guide. From key methods to industry applications, this post has it all. Don’t miss out—read the full post now!
How to Use Precision Machining:
Incorporating Precision Machining into manufacturing entails a strategic approach, where design, materials, and precision converge to create components of unparalleled quality.
Design Considerations for Precision Machining:
Utilizing machining effectively begins with meticulous design considerations. Engineers must factor in the intricacies of machining processes, ensuring that designs are optimized for precision manufacturing. From intricate geometries to material compatibility, a well thought out design is the cornerstone of successful precision machining.
Material Selection and Its Impact on Precision Machining:
The choice of materials plays pivotal role in the precision machining process. Engineers must carefully select materials based on their properties, considering factors like hardness, machinability and thermal conductivity. The synergy between design and material selection is crucial in achieving the desired precision and functionality in the final product.
Importance of Accurate Measurements and Tool Calibration in Precision Machining:
Precision in machining hinges on accurate measurements and calibrated tools. Regular tool calibration ensures that cutting instruments maintain their effectiveness, contributing to the consistency and reliability of the machining process. Accurate measurements, facilitated by advanced metrology tools are indispensable for meet the stringent quality standards.
Case Studies Showcasing Successful Applications of Precision Machining:
Illustrating the efficacy of accurate machining, case studies and examples provide real world insights. These success stories highlight how precision machining has been instrumental in achieving complex designs, ensuring product integrity and surpassing industry standards. From aerospace components to medical devices, these applications underscore the versatility and the impact of precision machining.
As manufacturers embark on the journey of using fine machining, this blueprint emphasizes the holistic approach required, where every step contributes to the creation of components that epitomize manufacturing excellence.
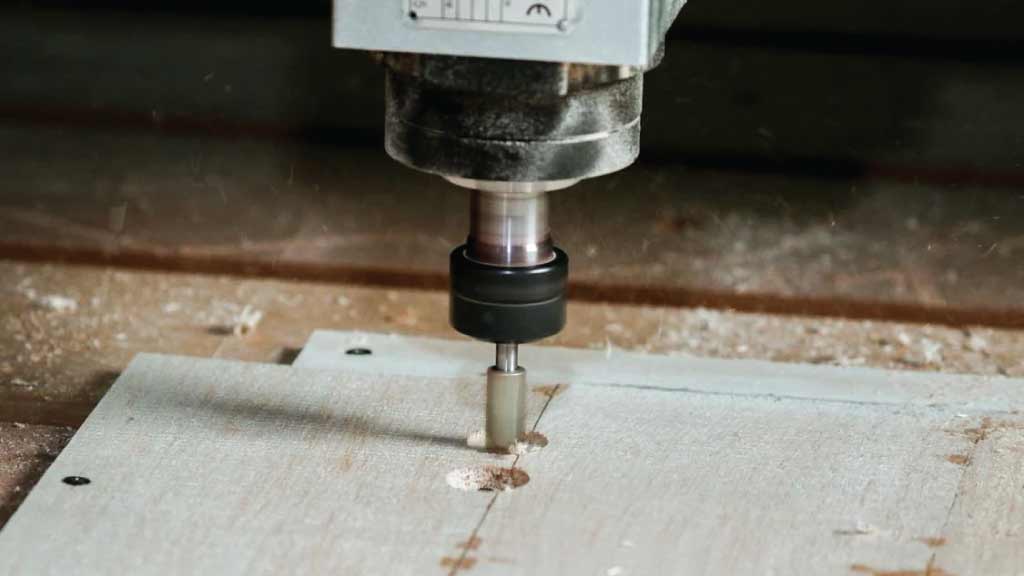
Precision Engineering Machining Challenges:
The realm of advanced machining, despite its undeniable advantages is not without its challenges. Manufacturers grapple with various hurdles and yet, the field thrives through innovative solutions and the technological advancements.
Common Challenges Faced in Precision Machining:
Precision machining encounters challenges that demand ingenuity and expertise to overcome. Common hurdles include tool wear, a persistent issue that impacts the lifespan and efficiency of cutting tools. Material inconsistencies pose another challenge, affecting the machinability of components and jeopardizing precision. Maintain tight tolerances, especially in intricate designs, requires meticulous attention to detail and precision.
Innovative Solutions and Advancements in Precision Machining:
The dynamism of precision machining lies in its ability to evolve and adapt. Innovative solutions continually emerge to address challenges head on. Advancements in tool coatings and materials enhance tool durability, mitigating the impact of wear. Automation and advanced CNC technologies optimize processes, reducing human error and enhancing precision. Adaptive machining strategies, guided by real time data analytics, empower manufacturers to navigate material variations effectively.
In summary, the challenges within precision machining serve as catalysts for innovation. The industry resilience is evident in its capacity to surmount obstacles through the inventive solutions and embrace technological progress. As precision machining continues to advance, the collaboration between human expertise and the cutting edge technologies paves the way for the future where challenges are not impediments but stepping stones toward unparalleled precision.
Benefits of CNC Precision Machining
CNC (Computer Numerical Control) precision machining is a widely used manufacturing process that brings numerous advantages to various industries. Here are some of the key benefits:
1- High Precision and Accuracy
One of the most significant advantages of CNC precision machining is its ability to achieve incredibly tight tolerances and accurate dimensions. Automated control systems ensure consistent production with minimal human error, making CNC machines ideal for complex parts that require high precision.
2- Enhanced Efficiency and Productivity
CNC machines are highly efficient, operating continuously 24/7 with minimal supervision. Once programmed, they can perform multiple complex tasks without interruption, reducing production time and increasing output. This allows for faster manufacturing and shorter lead times, which is critical for large-scale production.
3- Consistency and Repeatability
CNC precision machining delivers consistent results with every run. Whether producing a single part or a large batch, the machine replicates the same design accurately, ensuring uniformity across all products. This repeatability is essential for industries like aerospace, automotive, and medical manufacturing, where part consistency is crucial.
4- Complex Geometries
CNC precision machining allows manufacturers to create intricate shapes and complex geometries that would be difficult or impossible with manual machining. The multi-axis movement of CNC machines enables the production of sophisticated parts with detailed features, such as cavities, undercuts, and intricate curves.
5- Versatility in Material Use
CNC machines are capable of working with a wide range of materials, including metals, plastics, composites, wood, and ceramics. This versatility makes CNC precision machining suitable for various industries, such as aerospace, medical devices, automotive, and electronics, which require different types of materials.
6- Reduced Waste and Lower Costs
The high precision of CNC machining minimizes material waste. The machine removes only the necessary amount of material, leading to more efficient use of raw materials. This reduction in waste not only benefits the environment but also helps in reducing overall production costs.
7- Improved Safety
CNC machining reduces the need for direct human involvement in the manufacturing process, minimizing the risk of accidents and injuries. Operators program the machines and monitor the process remotely, creating a safer working environment, especially when dealing with dangerous tools and materials.
8- Flexibility and Scalability
Once the design is programmed into a CNC machine, it can be easily modified or scaled up for larger production runs. This flexibility makes it simple to switch between different product designs or increase production volume without significant changes to the machine setup.
9- Low Maintenance Requirements
CNC machines are generally low maintenance, requiring only periodic checks and calibration to maintain optimal performance. The automated nature of these machines also means fewer manual adjustments, reducing downtime and maintenance costs over time.
10- Faster Prototyping
CNC precision machining allows for rapid prototyping, where manufacturers can quickly produce prototypes for testing and design validation. This accelerates product development cycles and enables faster iteration on designs before mass production.
CNC precision machining offers numerous advantages, including high accuracy, efficiency, and the ability to handle complex designs and a variety of materials. Its consistent quality, low waste, and scalability make it an ideal choice for industries requiring precision, speed, and reliability in their manufacturing processes. This technology continues to revolutionize the way parts and components are made, enabling businesses to produce high-quality products with lower costs and faster turnaround times.
Future Trends in Precision Machining
The landscape of micro machining is undergoing the transformative shift, driven by the integration of automation and the advent of Industry 4.0. Emerging technologies are heralding the new era, redefining the possibilities and capabilities within precision machining.
Integration of Automation and Industry 4.0 in Precision Machining:
The future of high quality machining is intricately linked with the seamless integration of automation and Industry 4.0 principles. Smart factories, equipped with interconnected systems and IoT devices are revolution the manufacturing floor. Automation streamlines processes, enhances efficiency and ensures consistent, high quality outputs. Industry 4.0’s data driven approach empowers manufacturers with real time insights, enabling predictive maintenance and informed decision making.
Is Mechanical Engineering Hard? Many aspiring engineers wonder about the challenges in this field. Industrial Design also plays a crucial role in creating functional products. Please read our detailed and easy, ultimate guide on these topics to understand the demands and opportunities in these exciting careers. Don’t miss out—read the full post!
Emerging Technologies Shaping the Future of Precision Machine Manufacturing:
As we look ahead, several emerging technologies are poised to shape the future of precision machining. Additive manufacturing, often referred to as 3D printing is expanding its role, enable the production of complex geometries with unmatched precision. Artificial intelligence (AI) is enhancing process optimization and predictive modeling, elevating the accuracy and speed of machining operations. Advanced materials, coupled with innovative tool designs are pushing the boundaries’ of what can be achieved, opening avenues for more intricate and durable components.
In conclusion, the future of accurate machining is marked by synergy between automation, data driven insights and cutting edge technologies. As Industry 4.0 unfolds, manufacturers embracing these trends are poised to not only meet but exceed the demands of precision and quality in the ever evolving landscape of manufacturing.
What Are Precision Machining Tolerances?
Precision machining tolerances refer to the allowable deviation from a specified dimension during the machining process. In other words, tolerances define the acceptable range of variation in a part’s size, shape, or other critical features without affecting its functionality. Precision machining tolerances are crucial in ensuring that components meet the required standards of fit, performance, and safety, especially in industries like aerospace, automotive, medical, and electronics.
Here’s a detailed look at precision machining tolerances:
Types of Tolerances
Precision machining tolerances are typically classified into three main types:
Linear Tolerances: These specify the allowable deviation in straight-line dimensions, such as length, width, or thickness.
Geometric Tolerances: These address the allowable variation in a part’s shape, orientation, or location. Common geometric tolerances include flatness, roundness, parallelism, and concentricity.
Angular Tolerances: These define the permissible deviation from a specified angle, ensuring that parts are aligned or oriented correctly.
Tolerance Grades
Tolerances are often specified using standardized grades or classes, such as those defined by ISO (International Organization for Standardization) or ANSI (American National Standards Institute). These grades indicate the degree of precision required for a particular component, with tighter tolerances representing higher precision.
Standard Tolerances: Typically in the range of ±0.005″ to ±0.010″ (0.127 mm to 0.254 mm), these tolerances are acceptable for less critical parts or those that don’t require exact precision.
Tight Tolerances: Tight tolerances can range from ±0.0001″ to ±0.001″ (0.0025 mm to 0.025 mm). These are used in applications where precision is critical, such as in aerospace or medical device manufacturing.
Importance of Tolerances in Precision Machining
Precision machining tolerances are vital for ensuring that parts function properly when assembled. Here are some key reasons why they are important:
Interchangeability: Parts produced with consistent tolerances can be easily replaced or interchanged, reducing downtime and maintenance costs in industries like manufacturing and automotive.
Fit and Function: Tolerances ensure that parts fit together correctly, preventing issues such as excessive friction, misalignment, or component failure.
Safety and Reliability: In critical applications, such as aerospace or medical devices, tight tolerances are necessary to ensure safety and reliable performance under stress or extreme conditions.
Factors Affecting Tolerances
Several factors can influence the achievable tolerance in precision machining, including:
Material Properties: Different materials, such as metals, plastics, and composites, respond differently to machining processes. For example, softer materials like aluminum may require larger tolerances than harder materials like stainless steel.
Machining Method: The method used (e.g., CNC machining, grinding, EDM) affects the achievable precision. CNC machining, for example, allows for extremely tight tolerances, while traditional methods may have more limitations.
Tool Wear: Over time, cutting tools wear out, which can affect the precision of the part being machined. Regular tool maintenance and calibration are necessary to maintain tight tolerances.
Environmental Factors: Temperature changes and vibrations during machining can cause material expansion or contraction, impacting the final tolerance.
Common Tolerance Ranges
Different industries and applications may require varying levels of precision, but some general tolerance ranges include:
General Machining: ±0.005″ to ±0.010″ (0.127 mm to 0.254 mm)
Precision Machining: ±0.001″ to ±0.005″ (0.025 mm to 0.127 mm)
Ultra-Precision Machining: ±0.0001″ to ±0.001″ (0.0025 mm to 0.025 mm)
Precision machining tolerances are critical in ensuring that parts meet the required specifications for fit, performance, and safety. Achieving the correct tolerances depends on factors such as material, machining method, and tool condition. Understanding and applying the appropriate tolerances is essential for industries where precision is a key requirement, ensuring that components work reliably and efficiently in their intended applications.
Explore the various types of manufacturing equipment, their essential uses, and maintenance tips in this insightful guide. Stay informed and keep your operations running smoothly—read the full post
Precision Machining Examples
Precision machining is used to create highly accurate parts and components in a wide variety of industries. The process typically involves advanced equipment such as CNC machines, lathes, and grinders, all of which ensure parts are manufactured to exact specifications with minimal deviation. Here are some common examples of precision machining applications across different sectors:
1. Aerospace Components
The aerospace industry requires precision machining to produce complex parts that meet stringent safety and performance standards. Examples include:
Jet engine components: High-tolerance parts such as turbine blades, engine housings, and compressor disks, made from durable materials like titanium and nickel alloys.
Landing gear parts: Machined components that support the landing mechanism, which must withstand extreme forces.
Avionics components: Precision-machined electronic parts and casings used in navigation and control systems.
2. Medical Devices and Implants
Precision machining plays a vital role in producing highly accurate medical devices and implants that ensure patient safety. Examples include:
Surgical instruments: Tools like scalpels, forceps, and clamps that must be machined with extreme precision for delicate medical procedures.
Orthopedic implants: Hip and knee replacement parts, dental implants, and other prosthetic devices made from biocompatible materials such as titanium or stainless steel.
Medical device housings: Precision-machined enclosures for devices like pacemakers, diagnostic equipment, and infusion pumps.
3. Automotive Parts
The automotive industry uses precision machining to manufacture components that ensure the reliability and safety of vehicles. Examples include:
Engine parts: Pistons, cylinders, crankshafts, and camshafts that require tight tolerances to function efficiently and withstand high temperatures and pressure.
Transmission components: Gears, shafts, and clutches that must fit together seamlessly to transmit power effectively.
Brake system parts: Precision-machined brake calipers, rotors, and drums that ensure proper braking performance.
4. Defense and Military Applications
Defense and military equipment often demand high-performance parts with exacting precision. Examples include:
Firearm components: Barrels, triggers, and receivers that require high accuracy to ensure reliability and durability.
Missile and rocket parts: Precision-machined parts for guidance systems, propulsion components, and structural supports used in advanced weaponry and defense systems.
Military vehicles: High-strength, precise components for tanks, drones, and other military vehicles.
5. Electronic and Semiconductor Components
Precision machining is essential in the electronics industry, where small, intricate parts must be manufactured with extreme accuracy. Examples include:
Printed circuit board (PCB) components: Microchips, connectors, and other parts used in electronics like smartphones, computers, and medical devices.
Heat sinks and enclosures: Precision-machined metal parts that provide thermal management for electronic devices and systems.
Semiconductor wafers: Components for semiconductor devices used in integrated circuits, often requiring sub-micron precision.
6. Optical and Laser Components
Precision machining is crucial for producing high-quality optical and laser components used in various industries. Examples include:
Lenses and mirrors: Precision-ground lenses and reflective surfaces used in cameras, telescopes, and medical imaging equipment.
Laser housings and mounts: Machined parts that hold and stabilize laser diodes or optics for industrial, medical, and research applications.
Fiber optic connectors: Precision-machined components for fiber optic systems that require exact alignment for data transmission.
7. Energy Sector Components
In the energy industry, precision machining is used to produce durable and efficient parts for power generation and distribution systems. Examples include:
Turbine blades: High-precision components for gas, steam, and wind turbines that require tight tolerances to ensure efficient energy conversion.
Pumps and valves: Components used in oil and gas extraction, hydraulic systems, and power plants that need high accuracy to maintain safety and performance.
Nuclear reactor parts: Precision-machined components such as fuel rods, containment vessels, and control rods used in nuclear energy production.
8. Robotics and Automation
Precision machining is critical for manufacturing parts used in robotics and automation systems, where accuracy and reliability are paramount. Examples include:
Robotic arms and joints: High-precision parts that ensure smooth and accurate movements in industrial robots.
Actuators and sensors: Components that provide control and feedback in automated systems, requiring precise machining to function correctly.
Robot end effectors: Custom machined tools and grippers used by robots to interact with objects in manufacturing and medical applications.
9. Jewelry and Watchmaking
Precision machining is used in the luxury industry to create fine, intricate components for watches and jewelry. Examples include:
Watch components: Precision-cut gears, springs, and other mechanical parts that ensure the accurate functioning of high-end watches.
Engraving and detailing: Precision-machined designs and patterns for rings, bracelets, and other jewelry pieces.
10. Tooling and Dies
In manufacturing, precision machining is used to produce molds, dies, and tooling equipment for various industries. Examples include:
Injection molds: Precision-machined molds used in plastic injection molding to produce complex parts with consistent quality.
Press dies: Tools used to shape and cut materials in stamping and forging processes, requiring high precision to ensure proper form and function.
Precision machining is a versatile process that serves numerous industries, from aerospace to electronics. The ability to produce highly accurate and intricate parts with tight tolerances makes it essential for manufacturing components that require high performance, safety, and reliability.
Dive into the world of additive manufacturing, exploring its definition, types, and real-world examples in this informative post. Discover how this innovative technology is shaping the future—read the full post now!
Conclusion: Precision Engineering Machining
In conclusion, our journey through the intricacies of precision machining unveils its pivotal role in the modern manufacturing. Precision machining, encompassing CNC processes, turning and milling techniques, EDM and grinding, ensures the creation of high quality products with unmatched accuracy. This manufacturing cornerstone demands attention for its ability to overcome challenges through innovative solutions, ensuring seamless future.
As we recap the significance of machining, businesses are encouraged to adopt this transformative approach. The spotlight on design considerations, material selection and precise measurements showcases its indispensable role in enhancing product quality. This comprehensive exploration underscores the importance of integrating precision into manufacturing practices, promising not just precision but the future marked by excellence in every manufactured component.
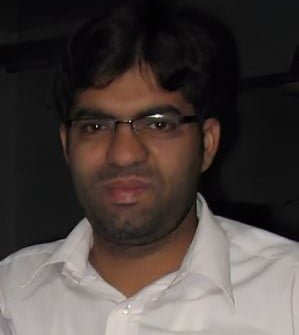
ZAK Engineer is an experienced engineer with 15 years in the mechanical and industrial sectors. Holding advanced degrees and multiple certifications in engineering, he combines technical expertise with a passion for writing to provide valuable insights into engineering innovations and business strategies. His content empowers professionals to excel in their fields and stay updated with the latest industry trends.
1 thought on “Precision Machining Explained: Everything You Should Know”